How to Create a Warehouse Management System for Your Logistics Business
Updated 11 Feb 2025
19 Min
413 Views
Warehouse Management System development can give end users and business owners everything they need to manage stocks, optimize space usage, streamline inventory processes, and save money. With the right approach, a well-designed WMS can enhance real-time visibility, reduce operational bottlenecks, and improve overall supply chain efficiency.
Dive deeper into our guide on warehouse management system development to learn what features and modules WMS should include, how much does it cost, how to improve it with AI, and so on. It will help you succeed in creating resilient software for improving inventory accuracy and increasing the efficiency of your warehouse workflows.
What is a Warehouse Management System?
A Warehouse Management System (WMS) is a type of logistics software that helps automate and optimize warehouse processes and tasks—tracking inventory, maximizing storage utilization, and efficiently running warehouse operations.
Real-time updates on inventory levels, status of shipment, and order fulfillment streamline your company’s logistics and reduce errors. WMS enables the enhancement of efficiency, control of costs, and end-to-end visibility during supply chain management.
Key WMS benefits for your business
Warehouse management software development allows you to reach the following advantages directly impacting your company’s productivity and, therefore, revenue.
- Faster order processing: You can utilize a WMS to process orders faster than manual methods and deliver shipments to customers on time, resulting in increased retention rates.
- Reduced operating costs: Through automation for picking, packing, and restocking, your company may reduce labor costs, which allows it to allocate resources more efficiently and minimize errors, leading to overall cost savings and improved profitability.
- Optimized space utilization: Smart slotting algorithms ensure efficient use of warehouse space for your logistics business, improving storage capacity.
- Improved inventory accuracy: A WMS helps maintain real-time inventory tracking, reducing stock discrepancies and preventing overstocking or stockouts.
Types of WMS
Picking the right WMS is determined by your business size, structure, and operational needs. Some solutions operate independently, while others are embedded in larger systems to manage workflows.
You can select one of the types of Warehouse Management Systems according to your business needs and requirements:
- Standalone WMS: Focuses only on your warehouse operations and works independently of other software
- Integrated WMS: Integrated as a part of building an ERP system from scratch
- Cloud-based WMS: Provides scalability and remote access without requiring on-site hardware
- Custom warehouse management software: Designed specifically for your exclusive workflows and operational demands
Warehouse operations to automate
Warehouse associates perform countless functions within a warehouse depending on what’s most needed. It may involve picking and packing goods, tracking inventory, scanning and tagging items, completing invoices, etc.
Let’s explore some other warehouse operations to automate.
Order processing
When a customer places an order, the WMS automatically verifies inventory levels, allocates items for the order, and updates inventory in real-time.
Inventory tracking
RFID and barcode scanning enable a WMS to track real-time inventory movements, reducing manual tracking.
Quality control
The WMS can automate quality control checks, triggering alerts and notifications for items not meeting quality criteria.
Shipping and labeling
When an order is ready, the WMS automatically generates shipping labels, packing slips, and necessary documentation. It also selects the most suitable shipping carrier based on predefined rules.
Returns management
The warehouse management system automates return authorization issuance, item inspection, inventory adjustment, and the refund or replacement process based on pre-set return policies.
After determining which warehousing processes to optimize, you must also specify the intricacies of the WMS operating mechanism to maximize the benefits of WMS implementation.
Operating mechanism of WMS
Look at the diagram below to understand how WMS deals with the major warehousing processes.
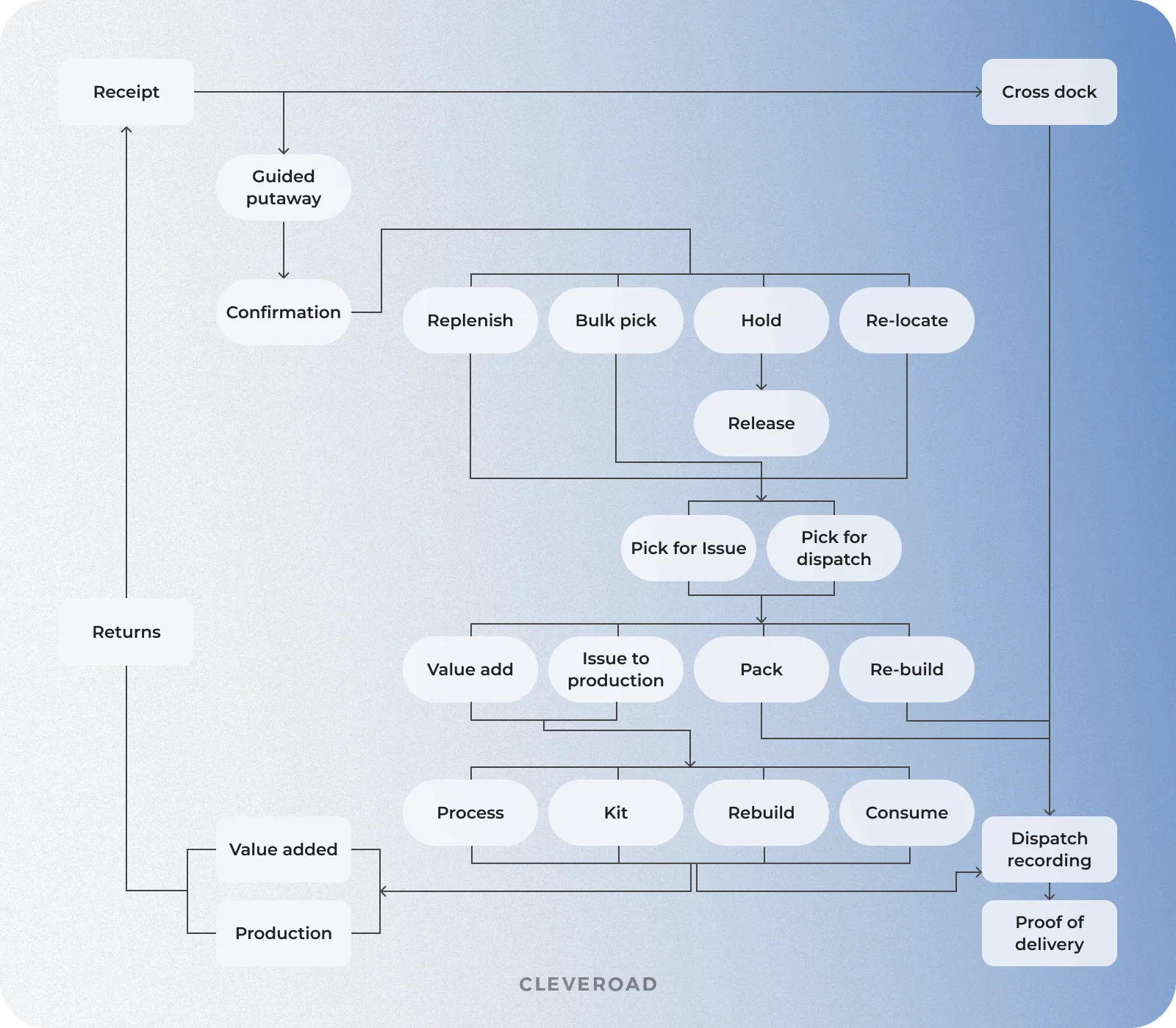
WMS functioning mechanism
When you develop a warehouse management system, you should remember that choosing the appropriate WMS technology is essential for improving warehouse processes, increasing efficiency, and ensuring accuracy in inventory management. Moreover, understanding key user roles within the system will enable smoother implementation and continued success.
User Roles Within Warehouse Management System Development
To help you better understand the parts you need to play in your WMS development, here is a short list of common warehouse roles and responsibilities.
Warehouse manager
The warehouse manager is the key player who supervises all facets of the warehouse operation. The managers have access rights to control all the operations they can perform in the WMS, such as inventory management, order processing, reporting, etc. They also work on keeping the operation running smoothly, looking for resources and processes to optimize the workflow and minimize operational expenses for your company.
Supervisor
The duties of a supervisor include planning, organizing, and overseeing the daily activities of warehouse workers to help them complete their assignments accurately and efficiently. It provides specialized customers with ship order tracking, inventory summary, purchase order, error processing, and performance monitoring.
Order picker/packer
Order pickers and packers play a crucial role in the custom warehouse management software development process by selecting suitable items and packing orders for delivery to individuals. Mobile devices enable warehouse pickers to scan barcodes, access warehouse management systems dynamically, and update the stock and order status in real-time.
As packers follow an order on a screen, they check the proper goods in the appropriate package and label them to be shipped when items are in stock. The packing screen simplifies printing ship labels, creating packing slips, scanning for bumps, and matching what has been shipped with the orders.
Receiver/client
The receivers and clients are the roles that help activate warehouses. Receivers perform inbound logistics by accepting, inspecting, and storing incoming shipments. Users (such as 3PL warehouse managers and B2B wholesale buyers) request access to showing inventory reports and search for available-to-promise data and number of orders. These positions collaborate to keep a warehouse functioning efficiently.
Additionally, a new warehouse must be flexible for omnichannel fulfillment and deliver a seamless experience across multiple sales channels, such as retail, e-commerce, and wholesale. It allows integrated inventory management and exertion processing across all the perches.
Distinctive user roles in WMS system development are essential as they force all stockrooms to cooperate in a coordinated manner and consummately integrate. Warehouse management data is crucial, so a warehouse management system development will help with accurate data management, from warehouse staffing to shop floor stock availability; WMS reports accurate differences as well as their resolutions.
Now, let us delve even deeper into the fundamental building blocks of the warehouse management system and how it interacts with the essential logistics architecture stations that lead to an optimal design response.
Features and Modules For Custom Warehouse Management Software
Let’s look through the list of the core WMS functionality modules.
Receiving module
This module streamlines accepting and recording incoming inventory. It verifies that received goods match purchase orders and determines optimal storage locations. Additionally, it ensures thorough inspection and validation of item quality.
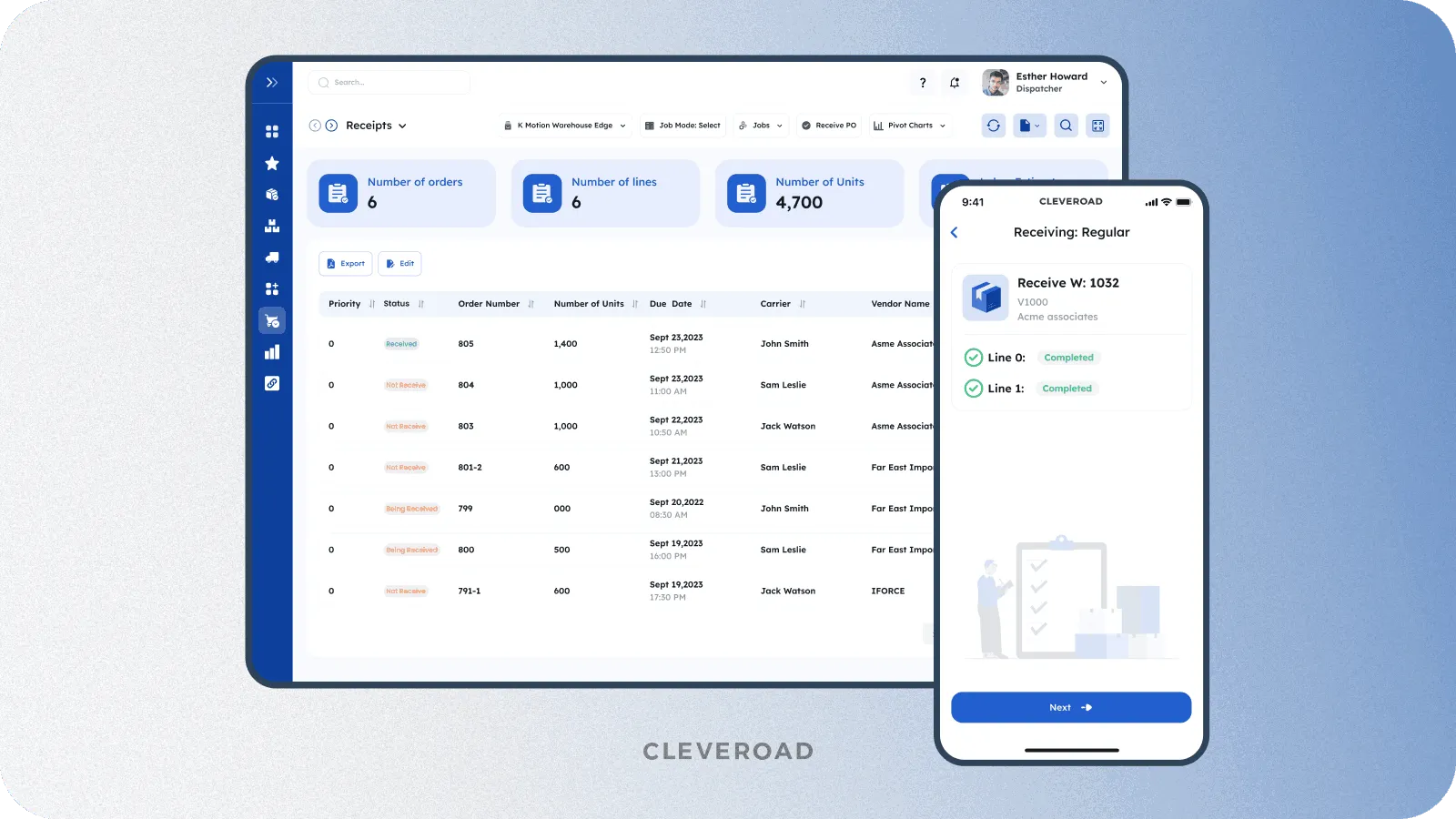
Example of receiving WMS module created by Cleveroad
Inventory management module
It maintains accurate stock levels and optimizes space utilization. It enables real-time inventory tracking and systematic stock counting. Additionally, it provides recommendations for reorder points and storage locations.
! Kindly note that instead of creating an inventory management module for your warehouse system, you can also proceed with the separate inventory management software development, and then integrate it with your WMS. The separate inventory management software allows you to streamline and optimize your warehouse operations, ensuring that inventory levels are accurately tracked, as well as reducing the risk of stockouts or overstock situations.
Order fulfillment and management
The order fulfillment and management module enhances accuracy, speed, and customer satisfaction in order processing. It captures and records orders in real time while classifying customers by priority. High-priority orders are processed promptly to improve service.
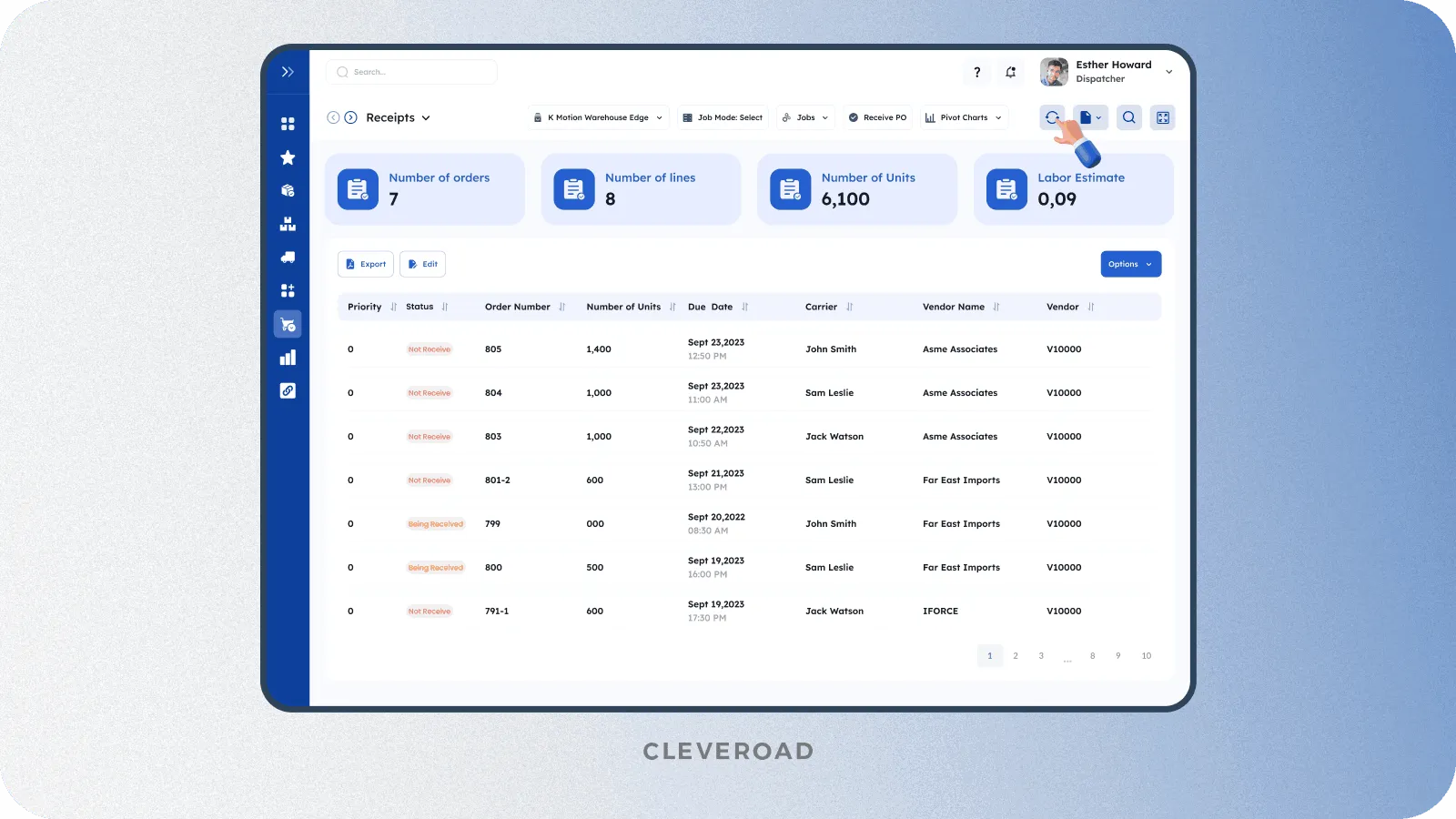
Order management module developed by Cleveroad
Analytics module
This module provides detailed reports tailored to warehouse needs. Users can create custom reports and forecast trends using historical data. As part of warehouse management software development, predictive analytics helps optimize staffing and anticipate demand fluctuations.
Advanced picking and shipping
It improves order fulfillment accuracy and efficiency, guides warehouse staff through the picking process and enables multi-order picking. Additionally, this module automates shipping, including label generation and tracking.
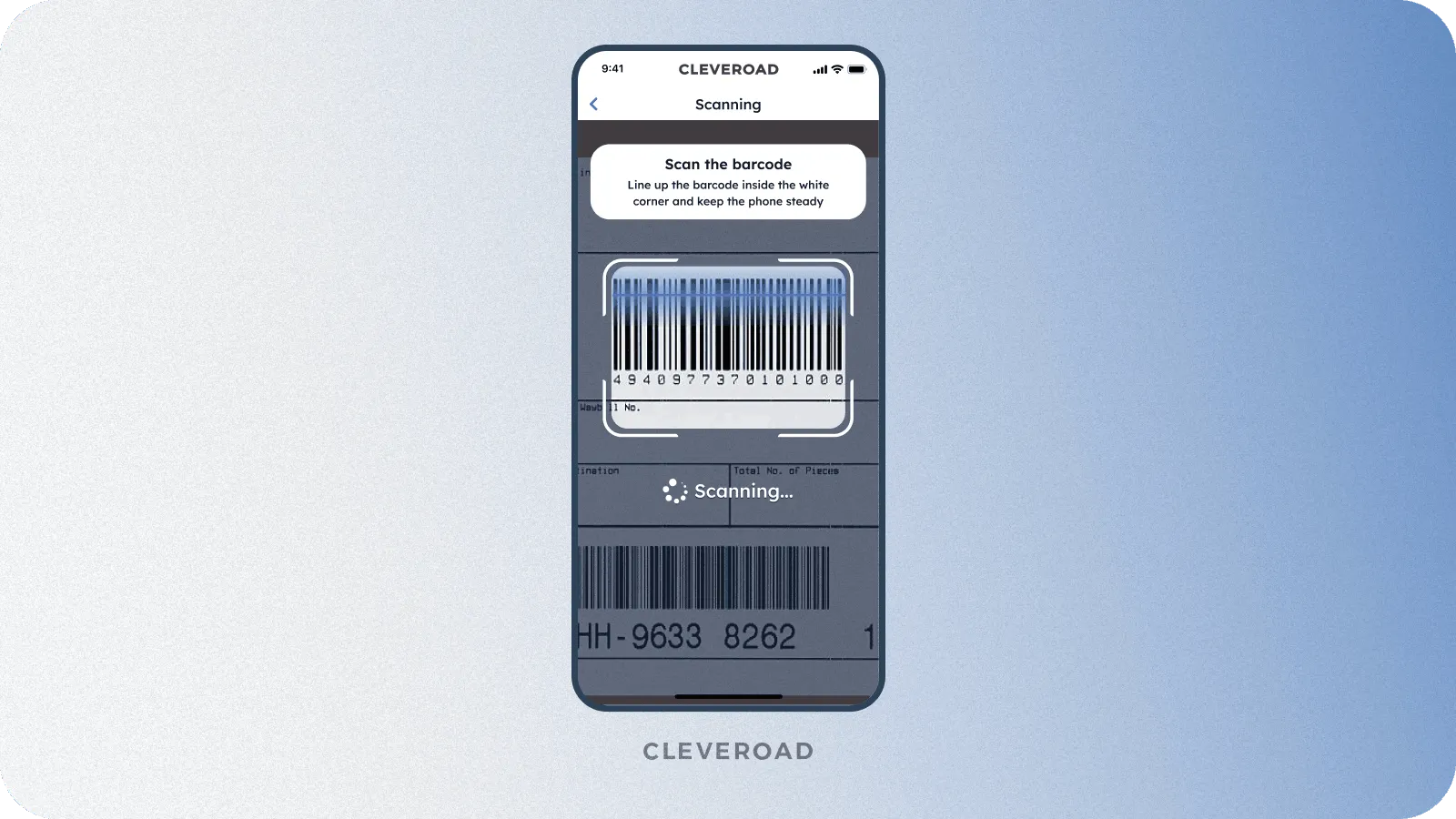
Barcode scanning feature example during shipping the items created by Cleveroad
Automatic data-sharing prioritization
This module ensures seamless integration with ERP systems and third-party applications. It enables real-time data exchange with suppliers and customers. What is more, it facilitates electronic document exchange for automated transactions.
We’ve described only the critical feature modules required for your WMS system’s seamless functioning as well as the warehousing automation for your logistics flows. You should understand that the ultimate functionality list depends on your business requirements and needs.
Choosing the feature set for your future WMS is complex and responsible, as your business performance and success depend on this choice. You can facilitate this task and contact us for an in-depth consultation. Our domain experts will guide you on how to create a warehouse management system and make an entire WMS feature set based on the needs of your shipping company.
How to Improve Custom Warehouse Management Software Development with AI
How does AI help in manufacturer warehouse management? The AI-integrated custom warehouse management system allows companies to perform predictive learning, error reduction, and customized operation optimization. The correct AI solutions accelerate speed, reduce price, and improve efficiency.
We’ll help you explore the most essential AI technologies to empower your warehouse operations.
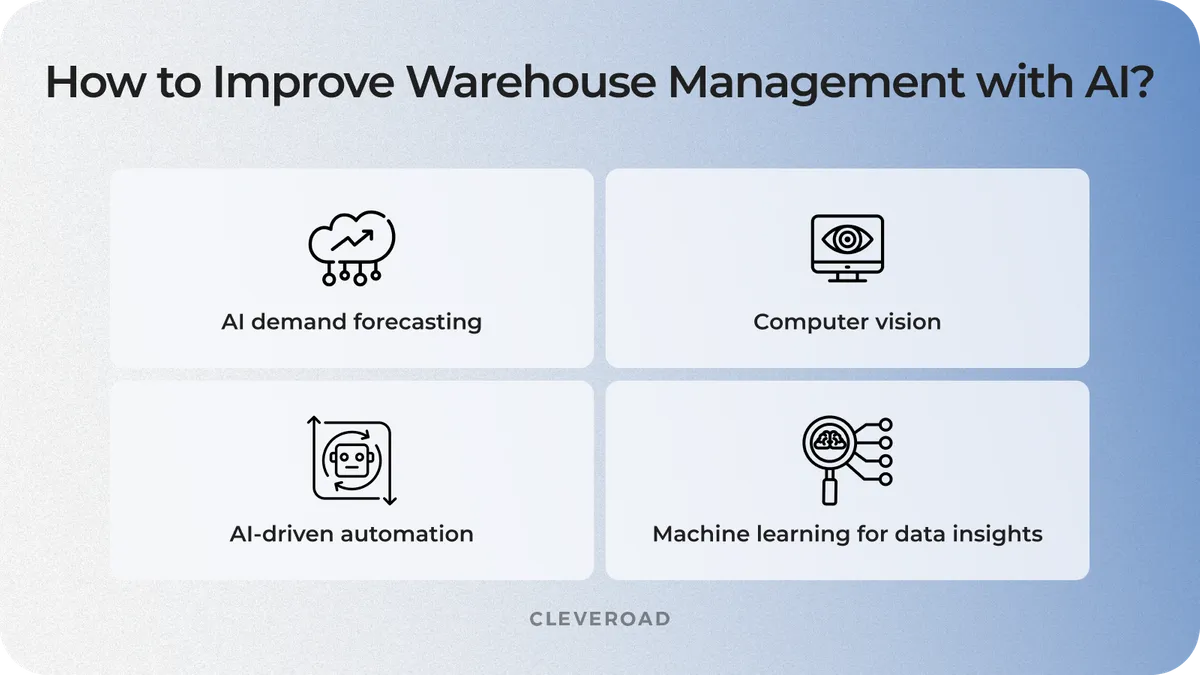
Improving custom WMS system with AI
AI for demand forecasting
When warehouse workers use AI forecasting in organizations, it responds much quicker to market and customer demand changes so that they can see into warehouse logistics. AI uses historical sales, market trends, and real-time data to predict demand. You can leverage these insights to ensure the correct items are in stock at the appropriate moment.
Forecasting by AI implemented in your custom warehouse management software reduces stock-outs or excess inventory. It boosts the order fulfillment rate and cuts down on unnecessary storage costs.
Computer vision for inventory accuracy
Inventory tracking with computer vision is more accurate than via manual means. AI-empowered cameras read barcodes, RFID tags, and dimensions of items to prevent inventory counting errors. The system provides instant detection of lost items and inventory discrepancies.
It means businesses can remove counting errors and lower shrinkage with up-to-the-minute monitoring. If you use a cloud-based warehouse management system, you can improve accuracy further as it can provide you with instant data access at multiple locations.
Find out the peculiarities of a smart warehouse management system to know what technologies can enhance your warehouse efficiency!
AI for tasks automation
AI helps automate repetitive tasks, including picking, packing, and sorting. Automated robots and systems process orders quickly and with minimal human error. AI-based route optimization reduces travel time in the warehouse. Intelligent algorithms distribute work according to worker availability and workload in custom warehouse management software. Companies achieve higher productivity using fewer resources, streamlining warehouse labor management.
Machine learning for data analysis
Warehouse data passes through analysis by machine learning to find patterns and inefficiencies. Logistics businesses use these insights to optimize workflows and improve decision-making. AI identifies bottlenecks, recommending real-time adjustments. Predictive insights optimize labor allocation and enhance warehouse layout efficiency. You can properly support agility and scalability since these insights are available anywhere through a cloud-based warehouse management solution.
Reliable warehouse management system support is crucial for AI-driven systems to work well. Regular updates, further troubleshooting, and interaction with emerging technologies keep the gears ticking. Artificial Intelligence improves WMS development efficiency by forecasting requirements.
The functionality of warehouse management solutions defines how effective they can be in optimizing operations and increasing efficiency. AI-enabled systems improve warehouse management through optimized inventory control, labor allocation, and real-time data analysis. In the competitive landscape of today’s fast-paced supply chain world, companies that leverage AI-powered insights for warehouse operations have greater success.
Consider the advantages of a customized WMS creation with our Warehouse Management System development services!
How to Build a Warehouse Management System?
Based on our logistics software development experience, we’ve prepared a comprehensive algorithm on how you should act when creating a digital product to manage your warehousing operations.
Step 1. Review your existing warehouse operations
A thorough review of your existing warehouse operations is critical. Start with an assessment of how your warehouse operates on a day-to-day basis from receiving and storing inventory to order fulfillment and shipping. This is important as accurate inventory tracking is key to minimizing errors and losses. Speak to relevant stakeholders (e.g., warehouse managers, supervisors, and staff that work directly in the warehouse) to understand their pain points.
Visibility into warehouse activities helps in better decision-making and resource allocation. This understanding will assist you in drafting a feature list based on warehouse management system features later.
Step 2. Select a trustworthy logistics IT partner
A comprehensive evaluation process is important to go through when selecting a reliable WMS development partner for creating your warehouse management software.
Here are some factors to choose logistics vendor that you should keep in mind:
- Use professional websites like Clutch to research and identify potential logistics IT partners that have experience developing logistics solutions.
- Check if they have a deep understanding of supply chain software, especially how the solution aligns with more extensive logistics functions.
- Examine the experience of each possible IT partner verifying for case studies or success stories related to their previous work on warehouse management. If you use SAP Extended Warehouse Management at your company, ask the provider if they have worked with that platform seamlessly.
- Choose a logistics IT partner offering uninterrupted support of and updates for the developed warehouse management software.
- Choose partners experienced to implement the latest technologies including AI, ML, blockchain, and IoT to take the most out of your warehouse’s digital transformation.
- Look through the client testimonials to know more about your future WMS development partner.
There is what one of our clients from the logistics domain says about cooperation with Cleveroad team.
John Salmon, Founder at Unified Potential, Inc.dba MoveUP. Feedback about cooperation with Cleveroad
Following this algorithm, you can make an informed decision when choosing a logistics IT partner, ensuring a collaborative and enduring partnership that contributes to the success of your warehouse management software.
Step 3. Identify your key features and system needs
Share your operational needs and requirements in terms of user roles and key features with your chosen logistics vendor. Based on this assessment, the vendor’s team will specify the functionalities needed, such as real-time inventory tracking, barcode scanning, automated picking routes, order processing, or demand forecasting with AI support.
Providing clear goals about your logistics processes, integration needs and mobile access will help ensure that the final business solution meets your goals and improves overall productivity.
Step 4. Develop and test the WMS
Collaborate with your logistics IT partner to develop custom warehouse management software. Taking the predetermined requirements and feature list, development team will implement it in increments while testing everything along the way. Robust project management on vendor's end is necessary to keep the development going and you updated to review and provide feedback. A WMS has to perform perfectly in the physical world—at this point, a mistake can trigger chaos for entire supply chains. That’s why the system’s reliability depends on usability, security, and performance testing.
A well-developed WMS not only ensures operational efficiency but also provides centralized control over your entire inventory ecosystem. WMS offers advanced warehouse management features such as real-time tracking, automated workflows, and seamless integrations.
Utilizing code scanners enhances accuracy within the warehouse, reducing errors and improving productivity. These capabilities help businesses efficiently manage warehouse operations and optimize logistics.
As Sergey Molchanov explains:
Sergey Molchanov
Sales Team Lead at Cleveroad
"By building in a modern warehouse system for your business, you can get a platform to manage multiple stores from a single control panel. You basically get a “helicopter view” of your warehouse processes online and can seamlessly manage all your product listings, orders, and information pertaining to customers by means of a single, intuitive solution.”
Moreover, if required, the vendor’s developers integrate your WMS software with third-party logistics systems like the following:
- Enterprise Resource Planning (ERP) software development
- Transportation Management System (TMS)
- Warehouse inventory management software
- Supplier collaboration systems
- Order management software development
- Data Analytics and Business Intelligence (BI) Tools
- Voice Picking and Augmented Reality (AR) Solutions
- E-commerce platforms, etc.
However, if you already have a functioning warehouse management system and need to upgrade it with modern technologies and new functionality, you can also use our legacy systems modernization services.
Step 5. Integration and optimization of systems
A well-implemented WMS software allows for effective warehouse management and smooth daily operations. The development team installs the warehouse management system, integrates it with your existing logistics systems and configures user access.
Ultimately, seamless connectivity between these systems helps in inventory tracing, order fulfillment, and warehouse operations at large. Also important is training your personnel how to use the software effectively, as proper system adoption is essential to accuracy and efficiency in countless pick, pack and process operations.
Lastly, the vendor’s developers will provide help with WMS support upon your request, upkeep, or integration with other systems, like ERP and logistics platforms. Keep an eye on system performance, listen to user feedback, and optimize workflows to make decisions based on real-time data insights.
Challenges of WMS Development You Should Be Ready For
Let’s discuss the most widespread challenges of WMS software development and what you should know to solve them effectively.
Tech requirements for WMS
On WMS development, it is important to address a list of technical requirements to achieve efficiency, scalability, and smooth operations. It should be able to store and process large amounts of data quickly, and its design should support scaling as performance needs grow. Interoperability is crucial as it allows data to flow without barriers across all supply chain systems.
In the case of using enterprise data warehouses, it should enable the uniting of data from multiple sources in a centralized manner along with advance analytics support for the process optimization and decision making.
Regulatory compliance
Running a warehouse involves considering many rules, laws, and regulations that are the basis that helps perform a custom warehouse management software smoothly. We will closely examine these essential rules, decomposing them in a way that’s easy to understand. Let’s also cover everything from keeping employees safe to protecting the environment and managing inventory properly.
Regulation type | Description |
Hazardous materials handling | Warehouses dealing with hazardous materials must comply with regulations governing the storage, labeling, handling/disposal of dangerous substances to ensure employee safety and environmental protection. |
Chemical safety | Warehouses storing chemicals are subject to regulations that require proper labeling, segregation, and documentation of hazardous materials, as well as compliance with Occupational Safety and Health Administration (OSHA) standards. |
Quality standards | Various industries have specific quality standards and certifications (e.g., ISO 9001) that warehouses must meet to ensure the quality and safety of stored products, including components used in manufacturing. |
Customs and trade compliance | Warehouses involved in international trade must comply with customs regulations, including import/export documentation, tariff classifications, and compliance with trade agreements. |
Environmental regulations | Warehouses must adhere to environmental regulations, covering waste disposal, emissions, and energy efficiency measures to minimize their ecological footprint. |
Security standards | Security regulations dictate access control, surveillance, and intrusion detection systems to safeguard the warehouse and its contents against theft, vandalism, or unauthorized access. |
This table mentions only the most common regulations you need while developing WMS software. However, it should be noted that there are more specific regulations (e.g., foods, pharmaceutical ones) you need to comply with depending on the goods storing in your warehouse.
Dealing with warehouse management system development challenges requires not only a skilled logistics IT vendor’s help but also a budget for implementing technological know-hows and paying the specialists for their services.
Security in WMS development
A WMS handles sensitive business data, so security must be a top priority. We can protect your warehouse management system with robust encryption, access control, and real-time monitoring. Moreover, we define different user roles, implement multi-factor authentication, and run regular security audits to help identify and deal with potential vulnerabilities before they can be exploited. We secure the system and make it resilient by protecting operations, preventing data leaks, and ensuring compliance with the industry regulations.
By the way, Cleveroad obtained ISO 27001 standard certification that proves our ability to manage data security risks when developing warehouse management software for you.
Dealing with custom warehouse management software development challenges requires not only a skilled logistics IT vendor’s help but also a budget for implementing technological know-hows and paying the specialists for their services.
How Much Does It Cost to Develop a Warehouse Management System
Logistics software development specialists calculate the detailed price of a warehouse management system regarding functionality complexity, software type, integrations, design, and software development rates. If to sum up all of the above factors, the average custom WMS cost will be from $70,000 to $250,000+. However, you can get the exact number of budgeting from the IT experts if you have at least a required functionality set or can define a type of WMS you would like to receive.
Kindly note that you do not need to necessarily hire in-house software engineers to build a warehouse management system. You can hire a vast pool of outsourcing logistics IT experts to create a solution to manage your warehouse activities.
We’ve prepared a corresponding table to help you consider the approximate warehouse management system development team composition and outsourcing hourly wages for their services.
Specification | Central&Eastern Europe | Western Europe | North America | Latin America | Asia | Africa |
Developers | $50 - 60 | $30 - 65 | $80 - 100 | $35- 70 | $20 - 45 | $25 - 45 |
UI/UX Designer | $35 - 45 | $30 - 50 | $70 - 80 | $40 - 60 | $20 - 30 | $20 - 30 |
Project Manager | $50 - 70 | $30 - 50 | $70 - 80 | $40 - 60 | $20 - 30 | $25 - 35 |
Business Analyst | $25 - 35 | $25 - 45 | $60 - 75 | $35 - 60 | $15 - 25 | $20 - 30 |
QA Specialist | $25 - 40 | $25 - 45 | $60 - 75 | $35 - 60 | $15 - 25 | $20 - 30 |
DevOps | $30 - 50 | $30 - 65 | $80 - 100 | $35- 70 | $20 - 45 | $25 - 45 |
Team Lead | $45 - 55 | $45 - 65 | $85 - 110 | $45- 80 | $35 - 45 | $30 - 45 |
Looking through the table, you can see that the rates vary significantly worldwide. For example, developers from North America tend to have a higher rate, but the price does not necessarily reflect the quality of their service. Additionally, looking for WMS development specialists with the necessary skills and expertise in local markets can be challenging. Moreover, it can be an expensive option as you will have to compete for fair salaries.
Central and Eastern Europe is recognized for its proficiency in this field. Outsourcing warehouse management software development to Central European countries can result in lower rates and highly qualified developers. Numerous software development companies offer custom software solutions at an average rate of $50 to $70 per hour.
Furthermore, hiring globally allows access to diverse skilled professionals in various technologies, including those in high demand. As an example, one of the largest American tech companies, Google, utilizes outsourcing services for its numerous products and services.
As you can notice, warehouse management software development is a complex process depending on different constituents. So, you should gain the support of a qualified logistics software development vendor to succeed with your WMS development process.
Why Cleveroad Is the Right Choice for Warehouse Management System Development
Cleveroad is a skilled logistics IT company with 13+ years of experience in developing custom complex software for logistics providers, retailers, manufacturers, distributors, and wholesalers to improve workflow performance. Our digital solutions also help to enhance collaborations between shipping organizations, their partners, and customers.
Confirming our position as a reliable software development provider, Cleveroad got certified with ISO 9001 2015 standard certification (quality) and ISO/IEC 27001:2013 certificate (security). Moreover, in 2024, we ranked 7th among Clutch TOP-1000 business service providers, were acknowledged as Clutch Global and Fall 2024 Champion, and obtained a bunch of other prestigious awards.
Working with us, you will get a range of benefits for your logistics business:
- Hands-on experience in creating logistics solutions like Warehouse Management Systems (WMS), Transport Management Systems (TMS), Fleet Management Software, Inventory Management Software, and mores.
- In-depth knowledge in the integration of WMS software with external systems or third-party services (e.g., Xero, Salesforce, Google Maps, Logistaas)
- On-demand IT services: creating WMS solutions from scratch, legacy system modernization, IT consulting services, logistics software design, IoT implementation, etc.
- Free Solution Design Workshop with our logistics IT experts: Solution Architects, Business Analysts and Project Managers
- Flexible collaboration models to choose from: IT Staff Augmentation, Dedicated Development Team, Time and Material
- Signing a Non-Disclosure Agreement per your wish to protect your WMS software concept
To prove our expertise, we want to represent you one of our successful portfolio cases created for a logistics company — Transportation Management System (TMS).
Our customer is a long-distance freight transportation and storage company in the United States. To improve their control over shipments, automate route planning, and streamline warehouse operations, the organization needed to develop a turnkey digital solution. Furthermore, our client needed a smooth connectivity with their current business systems — the CRM and warehouse management system.
The team we formed designed and implemented a TMS platform tailored to the customer’s needs. The system enabled manual modifications and enhanced route planning. We also created an application for drivers to navigate along custom routes easily. Our team also succeeded in integrating TMS with other logistics systems to maintain data integrity and prevent duplication.
As a result, our client received a tailored TMS that reduced shipment losses and improved delivery times. By operating within a unified TMS environment, our client achieved their business goals and effectively increased profits.
Start benefiting from our hands-on experience in Logistics by building resilient and functional custom warehouse management software to optimize the space in your fulfillment center.
Warehouse Management System in Action: Solution Demo
Cleveroad team has designed a demo version of the Warehouse Management System, so you can view how the WMS system works on the example.
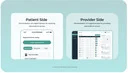
Warehouse management systems (WMS) development encompasses designing WMS software systems to enhance warehouse management through automation and real-time data monitoring.
A good software platform improves features of warehouse management systems, including inventory management, order processing, and shipping logistics. WMS also supports customer relationship management, due to which it has improved warehouse efficiency and improved labor management.
You will need to analyze the warehouse management FAQs to get closer to the best practices and suitable approach. Then build a plan for your specific warehouse based on layout, inventory tracking, and automation requirements. Finally, deploy software and processes that improve optimization for storage, order fulfillment, and real-time data monitoring.
There are four of warehouse management systems: standalone WMS, cloud based WMS, ERP-integrated WMS, supply chain modules. With a new WMS comes extensive automation and analytics capabilities that can lead to more efficient warehouse management through better use of inventory control and order fulfillment. WMS can help companies automate operations by integration with existing systems and improving features of a warehouse management process.
Launching a warehouse management system begins with reviewing existing processes and pinpointing opportunities for improvement in warehouse efficiency. A warehouse management system helps improve inventory monitoring and order processing by combining data and software for up-to-the-minute information. Selecting appropriate software to support operations guarantees smooth automation, while the right software helps optimize workflows and improve productivity.
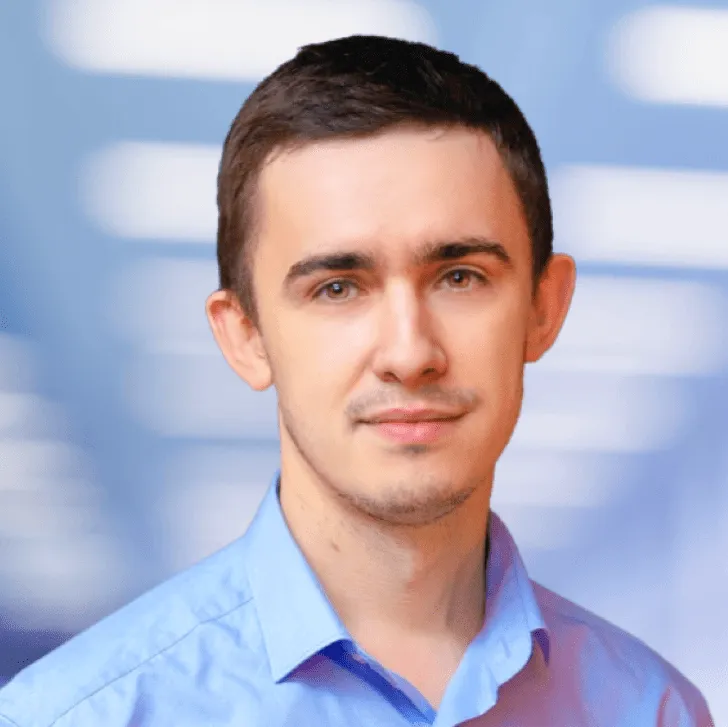
Evgeniy Altynpara is a CTO and member of the Forbes Councils’ community of tech professionals. He is an expert in software development and technological entrepreneurship and has 10+years of experience in digital transformation consulting in Healthcare, FinTech, Supply Chain and Logistics
Give us your impressions about this article
Give us your impressions about this article